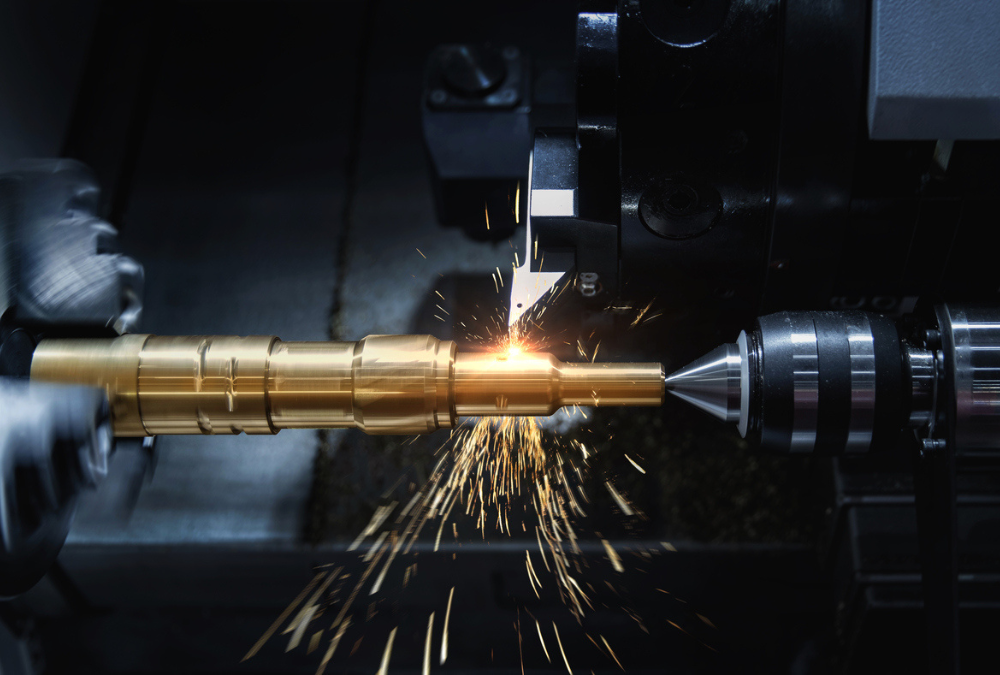
In today’s competitive industrial landscape, precision, speed, and quality are non-negotiable. That’s why companies across sectors rely on trusted CNC machining services to produce complex components with unmatched accuracy and repeatability. Whether you’re manufacturing prototypes or large-scale production parts, outsourcing CNC machining can save time, cut costs, and ensure exceptional quality.
What Are CNC Machining Services?
CNC (Computer Numerical Control) machining services involve using computer-controlled tools to manufacture precise parts from metal, plastic, or other solid materials. These machines operate on pre-programmed software to execute detailed cuts, drills, and shaping processes, transforming digital models into high-quality physical components.
Unlike traditional manual machining, CNC machining guarantees consistent precision—making it ideal for industries where quality and reliability matter most.
Core CNC Machining Processes
Modern CNC machining services typically include a combination of milling, turning, drilling, and other subtractive methods. Here’s a breakdown:
1. CNC Milling
Milling removes material from the workpiece using rotating multi-point cutting tools. This is suitable for producing flat surfaces, slots, and complex 3D shapes.
2. CNC Turning
Turning uses a stationary cutting tool and a rotating workpiece, ideal for cylindrical parts like shafts, bushings, and bolts.
3. CNC Drilling
Drilling is used to create accurate holes. CNC machines can also tap threads or countersink holes as required.
4. Wire EDM and Other Processes
Advanced CNC machining services may also offer Wire EDM (Electrical Discharge Machining) and grinding for ultra-precise or intricate components.
Industries That Rely on CNC Machining Services
Several sectors depend on CNC services for components that demand high tolerance, durability, and functionality:
Industry | Common Applications |
Aerospace | Engine parts, brackets, housings |
Medical | Implants, surgical instruments, diagnostic devices |
Automotive | Gears, manifolds, engine blocks |
Defense | Optical mounts, structural components |
Electronics | Enclosures, heat sinks, connectors |
Robotics | Frames, arms, drive components |
These industries count on CNC machining services to meet strict regulatory and performance standards.
Benefits of Outsourcing CNC Machining Services
1. Precision and Consistency
Top CNC machines can deliver tolerances of ±0.001 inches. Every part—whether it’s the first or the thousandth—is produced to exact specifications.
2. Cost Savings
Avoiding the overhead costs of owning and maintaining CNC machinery, hiring skilled machinists, and managing shop floors can result in major savings.
3. Speed to Market
Outsourcing speeds up production cycles. Rapid prototyping, fast tooling, and reduced in-house labor make project turnarounds much quicker.
4. Scalability
CNC machining services scale effortlessly from one-off prototypes to large production runs. Once the code is written, replicating parts is simple and consistent.
5. Material Versatility
Machining services typically support a wide range of materials, from aluminum and steel to brass, titanium, and plastics like ABS or Delrin.
Common Materials Used in CNC Machining
Choosing the right material is crucial for part performance and cost. Here are commonly machined materials:
Material | Properties |
Aluminum | Lightweight, corrosion-resistant, easy to machine |
Stainless Steel | Durable, strong, and resistant to rust |
Brass | Excellent machinability and electrical conductivity |
Titanium | Strong and lightweight, used in aerospace/medical |
Engineering Plastics | Good wear resistance, low friction, easy to cut |
Skilled machinists know how to optimize settings for each material to ensure efficient, high-quality production.
What to Expect from a Professional CNC Machining Service Provider
Not all CNC machining services are created equal. A reliable provider offers more than just part fabrication—they deliver engineering support, quality assurance, and consistent communication.
1. Design Support and DFM Feedback
Leading providers offer design-for-manufacturing (DFM) advice to improve manufacturability, reduce costs, and eliminate design flaws before production begins.
2. Prototyping to Production
From initial prototypes to full-scale manufacturing, top CNC shops can accommodate every stage of your product’s lifecycle.
3. In-House Quality Control
Trustworthy services employ quality inspectors and equipment like CMMs (Coordinate Measuring Machines), calipers, and micrometers to ensure parts meet strict tolerances.
4. Finishing Options
Additional services like anodizing, powder coating, polishing, and bead blasting help enhance functionality and aesthetics.
Popular CNC Machined Components
CNC machining is capable of producing a wide variety of components used in everything from industrial equipment to wearable tech.
Component Type | Typical Use Case |
Brackets | Mounting assemblies in vehicles or aircraft |
Housings | Electronics and sensors protection |
Shafts & Gears | Power transmission systems |
Valves & Fittings | Fluid and gas handling applications |
Custom Tooling | Manufacturing aids and jigs |
Custom CNC machining services can handle both standardized and uniquely designed parts.
Steps in the CNC Machining Workflow
Understanding the full CNC process can help you plan better and avoid delays.
Step 1: Design & Quoting
You submit a 3D CAD model, drawing, and technical requirements. The service provider reviews your design, offers feedback, and sends a quote.
Step 2: Programming
Engineers convert your design into G-code—software instructions that guide the cutting tools along precise paths.
Step 3: Material Selection & Setup
The selected material is mounted securely. Tooling and fixturing are prepared, and machine parameters are set.
Step 4: Machining
The CNC machine removes material layer by layer until the final geometry is achieved.
Step 5: Finishing & Quality Control
Parts are cleaned, finished, and inspected for dimensional accuracy, surface quality, and compliance with design specs.
Key CNC Machine Types Used in Services
Most CNC shops operate a mix of the following machines to serve diverse customer needs:
- 3-Axis Mills: Ideal for simple parts with limited angles
- 4-Axis Mills: Adds rotational capability for more complex geometries
- 5-Axis Mills: Allows machining on five faces in one setup
- CNC Lathes: Used for rotational parts and threading
- Swiss-Style Lathes: For high-precision, small-diameter components
Having access to multiple machine types allows providers to match the best equipment to your project.
Factors That Influence CNC Machining Costs
Several variables affect the pricing of your CNC machining project:
Cost Factor | Impact |
Material Type | Harder materials increase tool wear and machining time |
Part Complexity | Intricate designs take longer and require more setup |
Tolerance Requirements | Tight tolerances demand slower cuts and detailed inspection |
Quantity | Higher volumes reduce cost-per-part |
Surface Finishing | Secondary processes add to total cost |
A reputable CNC service provider will explain these factors transparently in your quote.
How to Choose the Right CNC Machining Services
Selecting the right partner for your machining needs is critical. Here’s what to look for:
1. Proven Track Record
Look for providers with experience in your industry and positive customer testimonials.
2. Fast Turnaround and Capacity
Can they meet your deadlines without compromising on quality?
3. Quality Certifications
Check if they hold ISO 9001 or other industry certifications. This reflects commitment to quality processes.
4. In-House Capabilities
A full-service shop with in-house design, machining, inspection, and finishing saves time and reduces risk.
5. Communication and Support
Clear communication, responsiveness, and technical support make for a smoother partnership.
CNC Machining vs. 3D Printing
While both technologies are valuable, CNC machining services are often the preferred choice for functional, load-bearing parts.
Factor | CNC Machining | 3D Printing |
Material Options | Wide range of metals and plastics | Limited industrial-grade materials |
Tolerances | Very tight (±0.001″) | Lower (±0.005″ typical) |
Surface Finish | Excellent, with post-processing options | Often rougher, needs extensive finishing |
Structural Strength | High | Generally lower due to layer bonding |
CNC machining offers reliability and strength that many industries require for mission-critical components.
Conclusion: Leverage CNC Machining Services to Stay Competitive
Outsourcing your part production to a trusted CNC machining services provider gives you access to world-class equipment, skilled technicians, and streamlined workflows. Whether you’re building custom enclosures, mechanical parts, or high-volume components, CNC services offer the precision and speed your business needs to thrive.
Investing in a reliable partner ensures you can focus on product innovation while they handle the details of manufacturing, consistently delivering quality on time and within budge.